Comprehensive Guide to Custom Internal Gear Services
1. Introduction
What Are Internal Gears and Their Importance?
Internal gears are gears with teeth on the inside surface of a cylindrical workpiece, meshing with external gears or pinions. They are essential in applications requiring compact designs and high torque transmission, such as planetary gear systems.
Why Choose Custom Internal Gears?
Opting for custom internal gears allows for tailored solutions that meet specific application requirements, ensuring optimal performance, efficiency, and longevity.
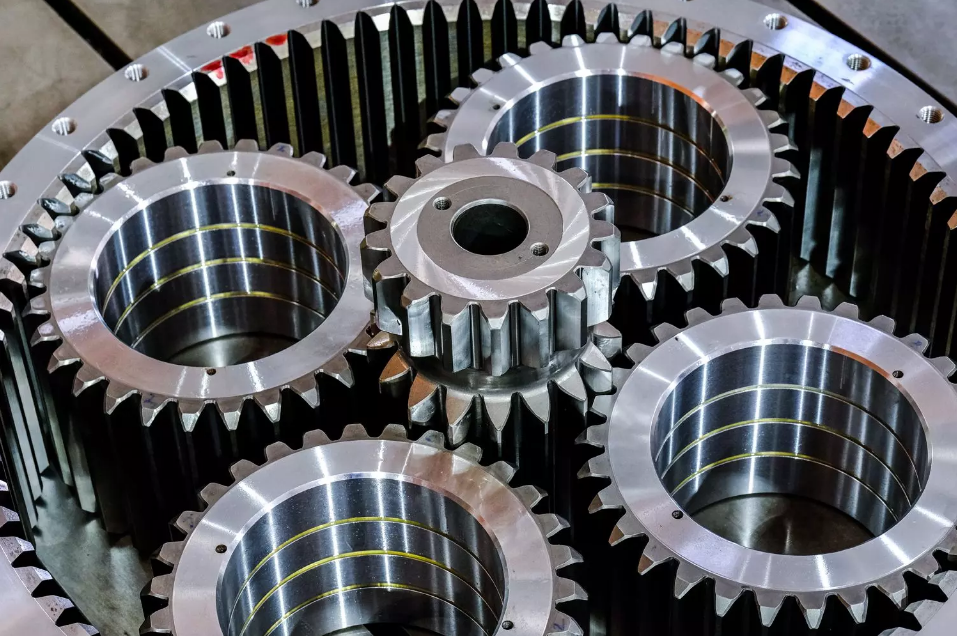
2. Advantages of Custom Internal Gears
• Compact Design: Internal gears enable more compact and efficient gear arrangements, especially in planetary systems.
• High Torque Capacity: Their design allows for higher torque transmission in confined spaces.
• Customization: Tailored specifications ensure compatibility with unique application needs.
• Noise Reduction: Properly designed internal gears can contribute to quieter operations.
• Durability: With appropriate materials and treatments, they offer enhanced wear resistance.
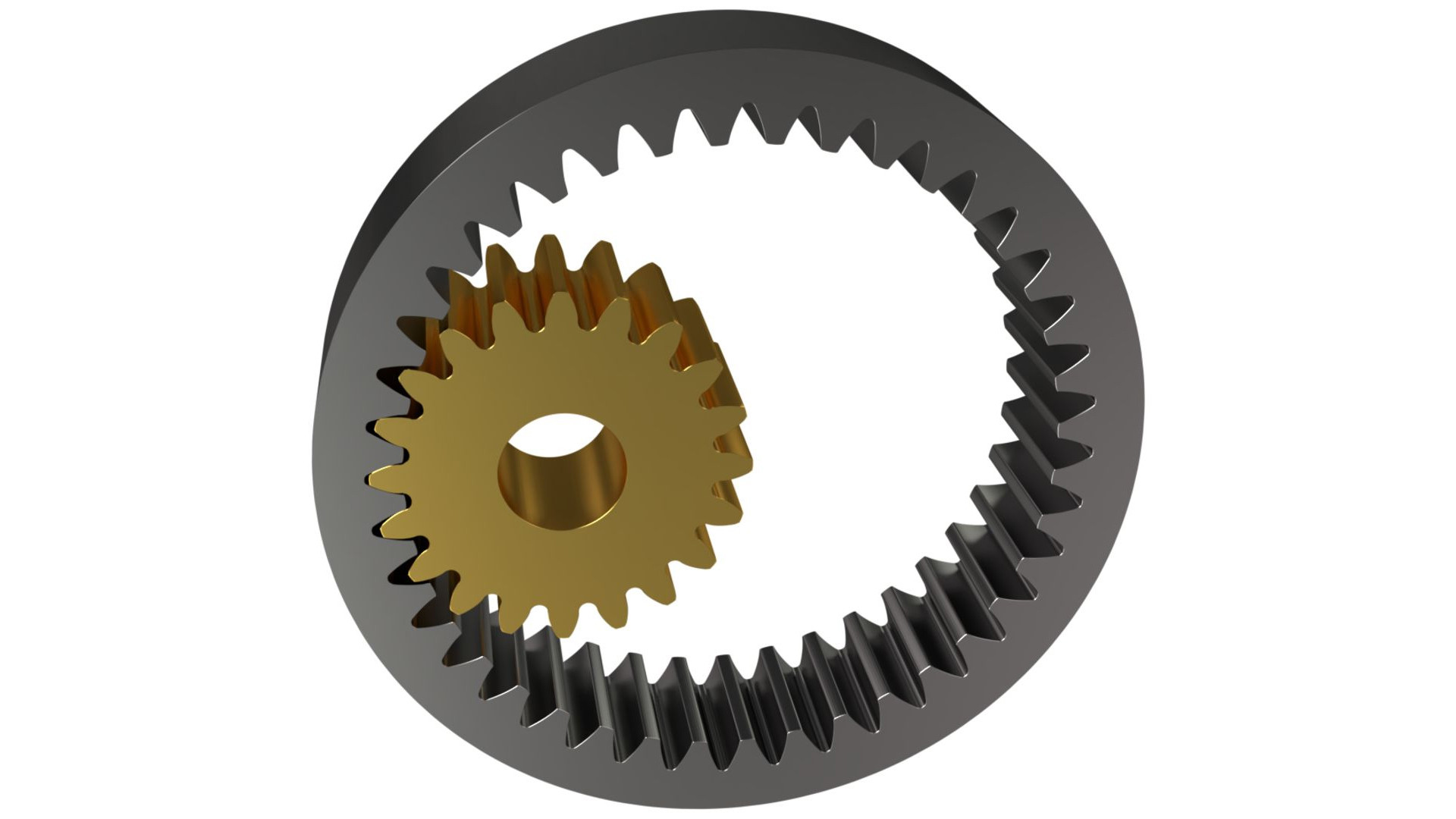
3. PairGears Custom Internal Gear Services
3.1 Personalized Design
We collaborate with clients to design internal gears that meet specific requirements, including tooth profile, module, and bore size.
3.2 Material Selection
We provide a range of materials, such as carbon steel, stainless steel, and brass, chosen based on the application's demands.
3.3 Size and Specifications
Our capabilities include producing internal gears with various modules, tooth counts, and pressure angles, tailored to your specifications.
3.4 Surface Treatment and Coatings
We offer surface treatments like nitriding and chrome plating to enhance wear resistance and extend gear life.
3.5 Advanced Manufacturing Techniques
• CNC Precision Machining: Utilizing advanced CNC machines for high-precision gear manufacturing.
• Gear Grinding: Achieving accurate tooth profiles and smooth surface finishes.
• Heat Treatment: Enhancing material properties for improved strength and durability.
3.6 Fast Response and Delivery
We ensure efficient project management to meet delivery timelines, accommodating both small and large orders.
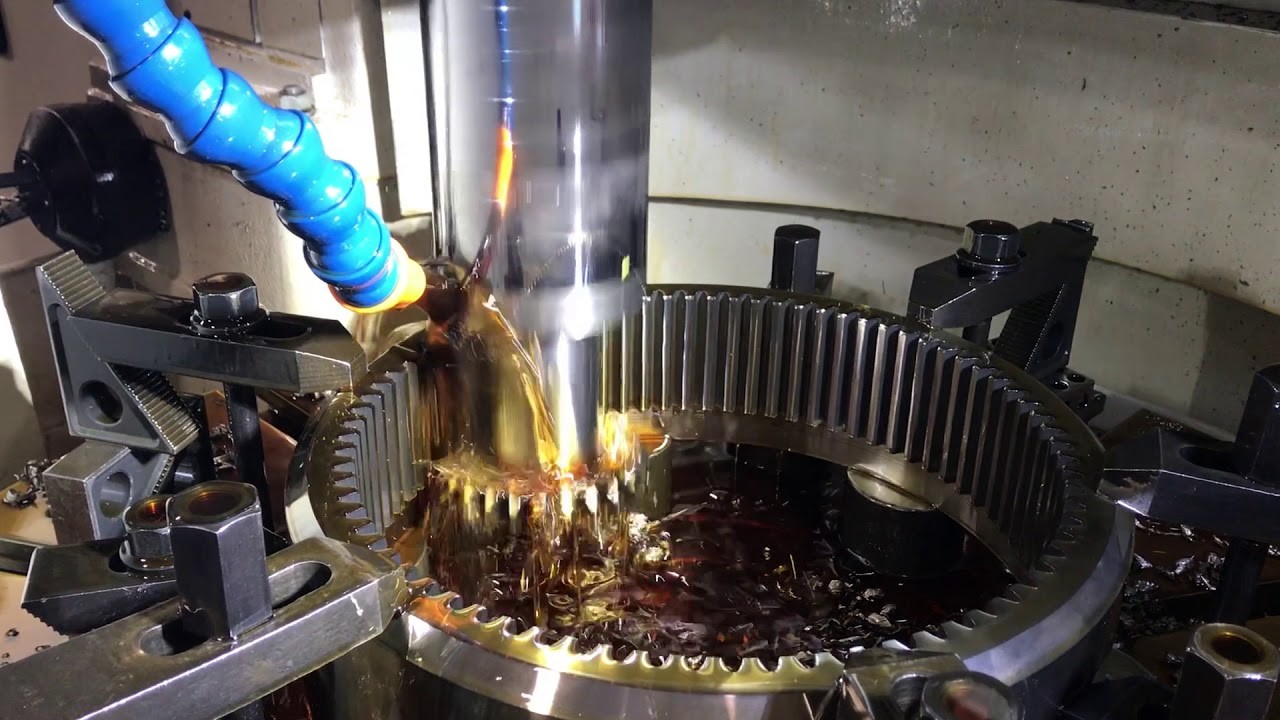
4.1 Design Parameters
Key factors influencing internal gear design include module, tooth count, pressure angle, and bore size.
4.2 Material Science
Selecting the appropriate material is crucial for performance. For instance, carbon steel offers strength, while stainless steel provides corrosion resistance.
4.3 Manufacturing Process
Our process encompasses:
• Gear Cutting: Utilizing methods like hobbing and shaping to form gear teeth.
• Heat Treatment: Processes such as carburizing to enhance hardness.
• Finishing: Grinding and honing to achieve precise dimensions and surface quality.
4.4 Surface Treatment
Surface treatments like nitriding and chrome plating are applied to improve wear resistance and extend gear life.
5.1 Strict Quality Testing Standards
We adhere to rigorous testing procedures, including hardness tests, dimensional checks, and surface roughness measurements, to ensure each internal gear meets high-quality standards.
5.2 End-to-End Monitoring
Our advanced monitoring systems track the production process from start to finish, ensuring precision and consistency in every batch.
5.3 Third-Party Certifications
PairGears is committed to meeting global standards, and our products are certified by ISO and other relevant international bodies, ensuring compliance with industry requirements.
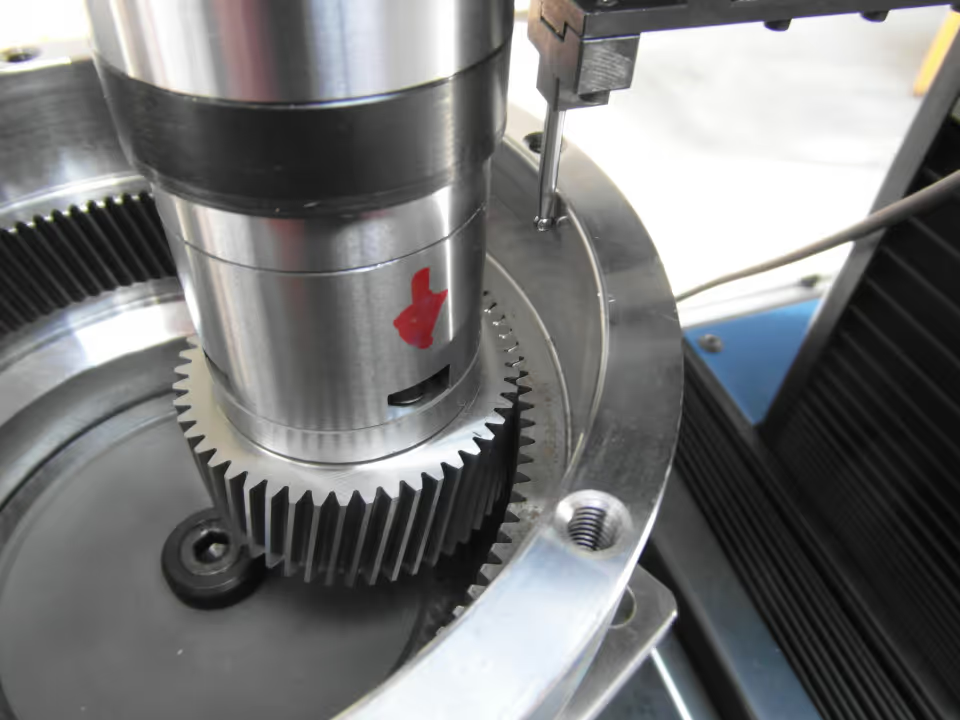
6. Applications of Custom Internal Gears
6.1 Automotive Industry:
Used in transmission systems.
6.2 Mechanical Engineering:
Employed in automation systems and robotic applications.
6.3 Aerospace:
Utilized in flight control systems and propulsion mechanisms.
6.4 Energy Sector:
Incorporated in wind turbines and hydroelectric generators.
6.5 Agricultural Machinery:
Applied in tractors and harvesting equipment.
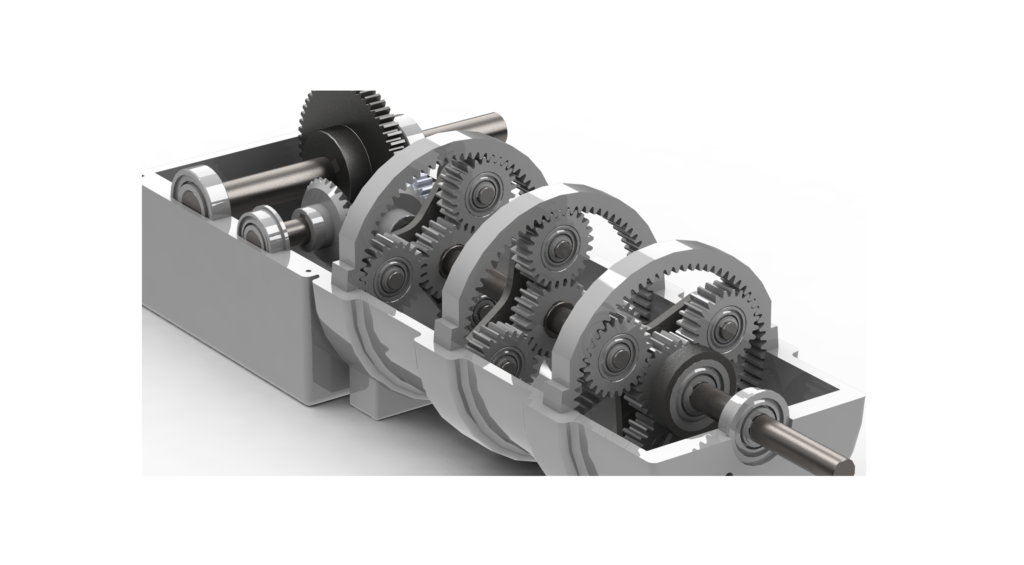
7. Case Studies
7.1 Automotive
We provided custom internal gears for a leading automotive manufacturer, enhancing the efficiency and reliability of their transmission systems.
7.2 Industrial Robotics
Our internal gears were integrated into robotic arms, contributing to smoother and more precise movements.
7.3 Agricultural Machinery
PairGears designed high-performance internal gears for a renowned agricultural machinery brand, optimizing their systems for higher load capacity and better reliability.
8. FAQ
Q1: What is the minimum order quantity for custom internal gears?
A1: The minimum order quantity depends on the specific product specifications. Please contact our sales team for detailed information.
Q2: How long is the lead time for custom internal gears?
A2: Lead time varies based on the order size and complexity. Typically, we complete orders within 30-45 business days after confirmation.
Q3: What material options are available for custom internal gears?
A3: We offer a range of material options including carbon steel, stainless steel, brass, and others, depending on your application needs.
Q4: Can you provide samples?
A4: Yes, we can provide samples based on your requirements, though a nominal fee may apply.
Q5: How do you ensure product quality?
A5: We adhere to strict testing processes and quality control standards, ensuring that every batch meets the highest industry standards.
Q6: What if I have special customization requirements?
A6: We are happy to accommodate special customization requests and will work with you to develop tailored solutions.
9. Start Your Custom Gear Project with PairGears
Custom internal gears are essential in ensuring the optimal performance and longevity of machinery across various industries. At PairGears, we are committed to providing high-quality, precisely manufactured gears that meet the unique needs of our customers. Contact us today to start your project.
Should you have any questions or require further assistance, please do not hesitate to contact our engineer: ben@pairgears.com.
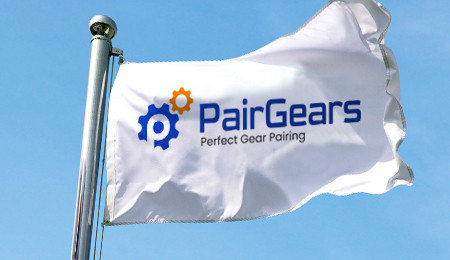