What is a Precision Gear? Everything You Need to Know
1. Introduction: What is a Precision Gear?
In the world of modern machinery, precision gears are fundamental components that ensure reliable power transmission, smooth operation, and minimal energy loss. But what exactly qualifies a gear as "precision"?
A precision gear refers to a gear that is manufactured to extremely tight tolerances, typically under ISO 1328 Class 3 to 7, allowing for high accuracy, quiet operation, and long-lasting performance in demanding applications. These gears are vital for industries like robotics, automotive, aerospace, and advanced agriculture equipment.
2. Key Characteristics of Precision Gears
2.1 Tight Tolerances
Precision gears are produced with micron-level accuracy in tooth geometry and overall dimensions. These gears must pass strict tolerance tests for tooth pitch, runout, and backlash.
2.2 Surface Finish
High-quality surface finishes reduce friction and wear, contributing to quieter and smoother gear engagement.
2.3 Material Quality
Precision gears are often made from hardened alloy steels, such as 20CrMnTi, 18CrNiMo7-6, or stainless steel, depending on load and environmental conditions.
2.4 Heat Treatment & Grinding
Heat treatment (carburizing, quenching, etc.) and precision gear grinding enhance hardness and profile accuracy, often necessary for high-torque or high-speed applications.
3. Common Applications of Precision Gears
• Robotics: for smooth and accurate movement.
• CNC machinery: to ensure accurate tool positioning.
• Electric vehicles: for quiet, efficient gear reduction.
• Agricultural equipment: such as tractors and harvesters.
• Aerospace: flight control systems and navigation drives.
4. Why Precision Gears Matter
Using a non-precision gear in a precision-demanding machine is like installing low-grade parts in a Swiss watch — it compromises performance, increases noise, and shortens service life.
With precision gears, you benefit from:
• Reduced vibration and noise
• Longer operating lifespan
• Higher load transmission
• Superior efficiency
5. How Precision Gears Are Manufactured
At PairGears, every precision gear is crafted under strict quality control. Here's how:
5.1 CAD-Based Design
Every gear is modeled using CAD/CAE software, ensuring exact tooth profiles and optimized geometry.
5.2 CNC Machining
We use 5-axis CNC machines to ensure precise cutting of gear blanks and tooth profiles.
5.3 Gear Grinding
High-precision grinding machines achieve up to DIN Class 4 accuracy.
5.4 Inspection and QC
Each gear undergoes CMM inspection, runout testing, and hardness verification before shipping.
6. Why Choose PairGears for Precision Gears?
PairGears specializes in custom precision gear manufacturing for international markets, serving OEMs and aftermarket distributors across Europe, North America, and South America.
Our precision gear offerings include:
• Spur gears
• Spur gears
• Helical gears
• Helical gears
• Shaft
• Sprocket
• Crown wheel and pinion sets
• Crown wheel and pinion sets
• Worm gears
• Synchronizers
• Internal Gears
What sets us apart:
• Fast sampling in 15 days
• Full ISO 9001:2015 compliance
• Support for small-batch customization
• Materials traceability and surface treatments like nitriding, black oxide, or zinc plating
Explore more at our Custom Gear Services page.
Conclusion
So, what is a precision gear? It’s the heart of accuracy in motion. Whether you’re designing an electric powertrain, a robotic arm, or an agricultural transmission, investing in precision gears ensures optimal performance, durability, and customer satisfaction.
If you’re looking for a trustworthy manufacturer of precision gears, PairGears is ready to support your next project — with accuracy you can measure and quality you can trust.
For inquiries or to discuss your specific gear requirements, please contact us.
Should you have any questions or require further assistance, please do not hesitate to contact our engineer: ben@pairgears.com.
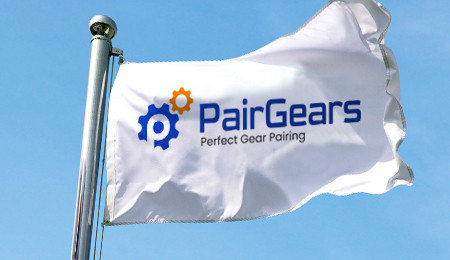